Project Description
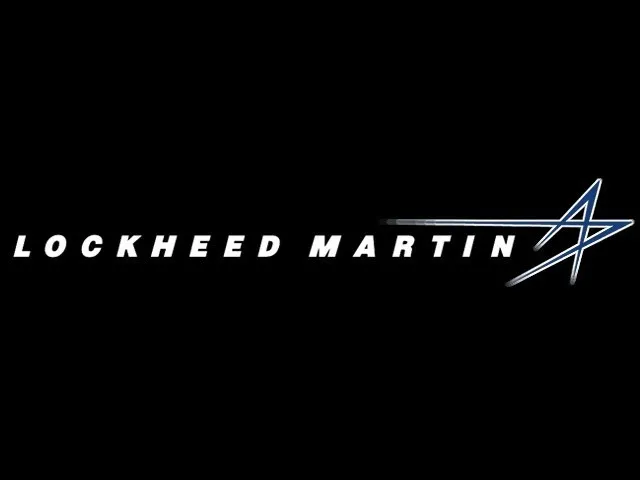
Working with Lockheed Martin, our team will design, test, and determine the best way to produce an additively manufactured (3D printed) cold plate to be used in various applications for the company’s numerous radar electronics. Components such as the FCBGA microelectronics are one of the primary sources of heat that must be diffused and thus will require a cold plate. The new cold plate should be designed to meet the needs of diminishing cost, monitor the amount of material used, and improve the current heat transfer efficiency. This is a critical design because products of Lockheed Martin’s can reach temperatures up to 1KW/cm². Furthermore, an effective cold plate must be prepared to dissipate this heat from the part. Our team is looking at numerous designs with complex geometric flow paths to be made. Additionally, the appropriate material is to be determined for manufacturing the cold plate while considering cost and functionality.
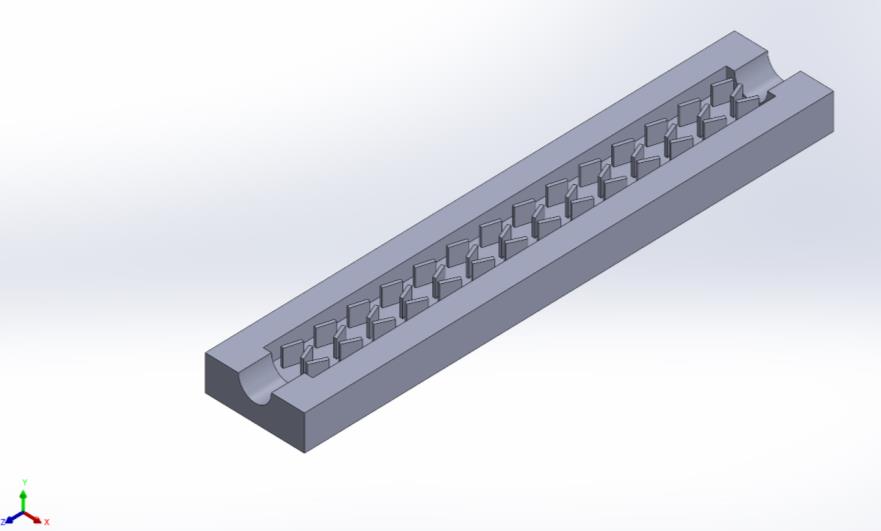
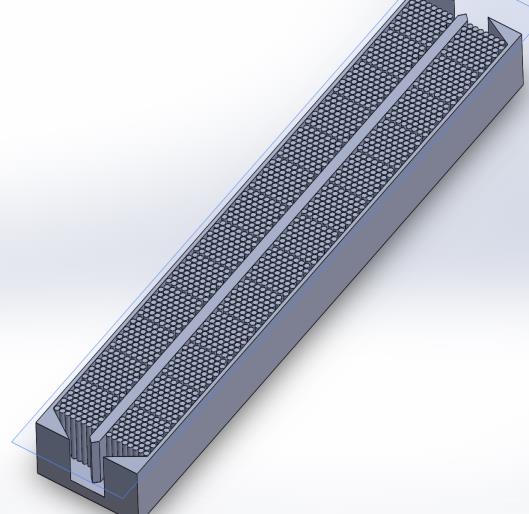
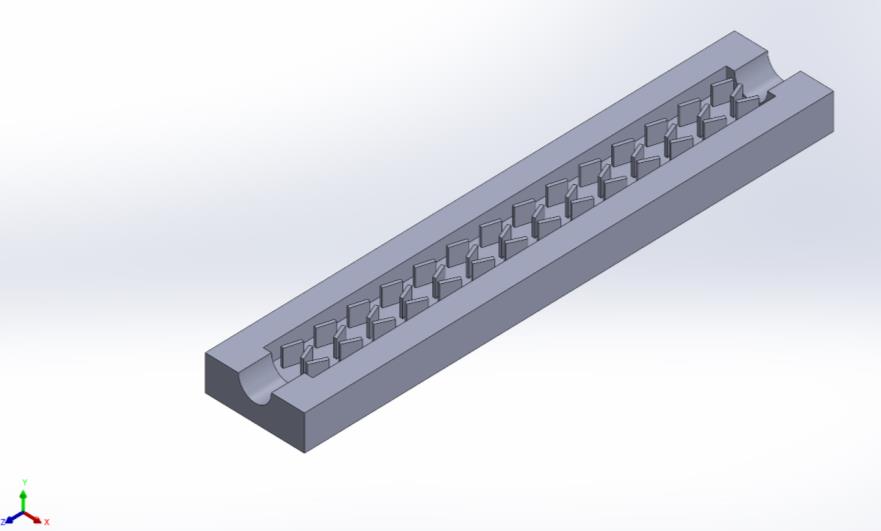
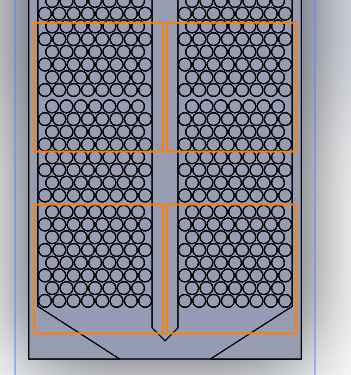
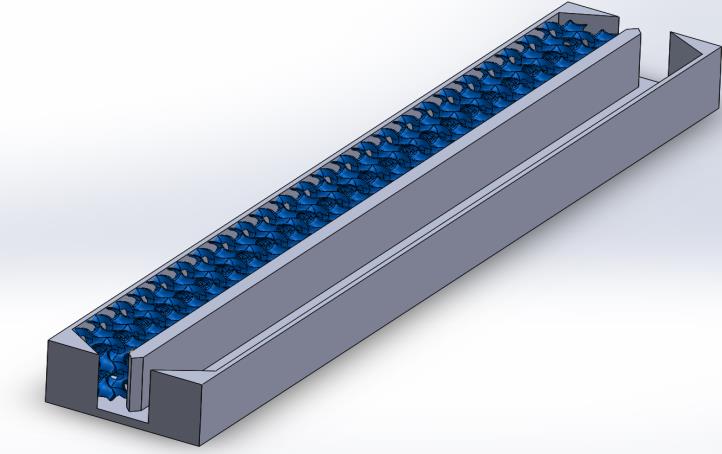
NTopology CAD Program
In initial research for this project, the team found a new CAD program called NTopology that has been used in many other additively manufactured designs. This program behaves much differently compared to other CAD programs like SOLIDWORKS and ANSYS Spaceclaim. This program uses equations to define cad bodies and lattices to aid in creating complex geometries and to allow ease of iterating designs. With that said, there is a very steep learning curve to using the program and creating an initial part, but once created the part can be manipulated with ease to allow for better analysis and for an overall better part design. Below are some of the capabilities and features that the team has designed with NTopology.
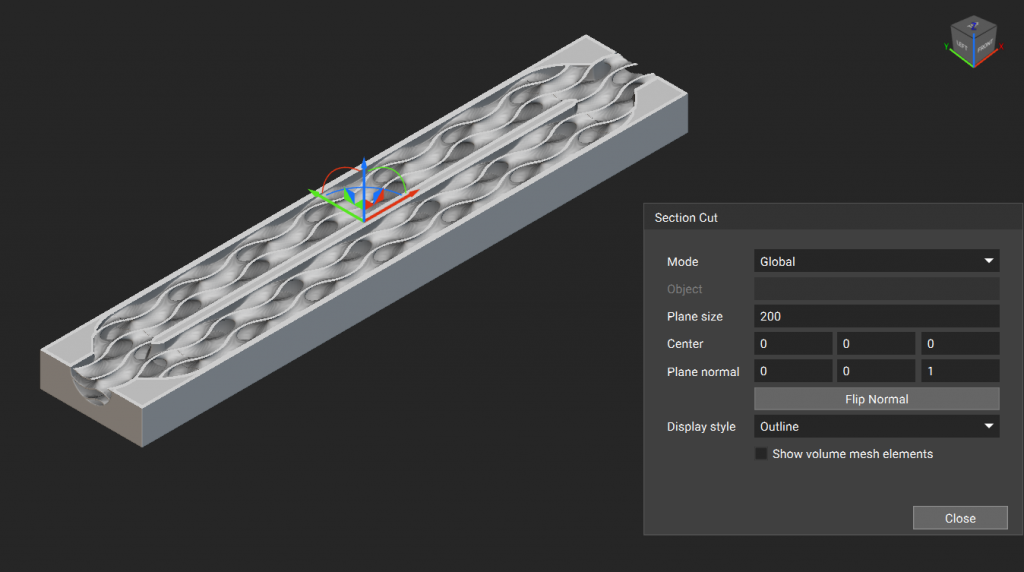
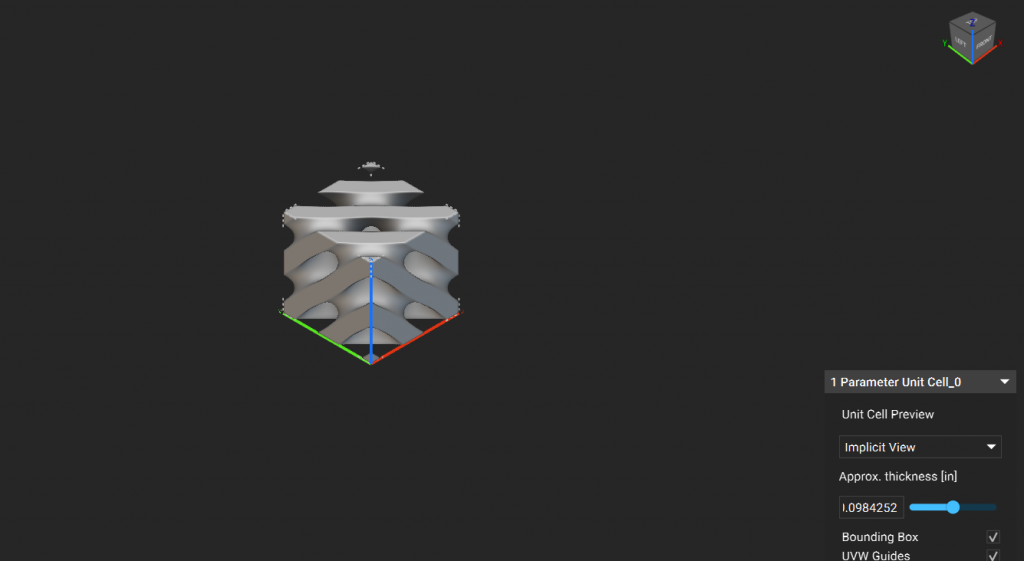
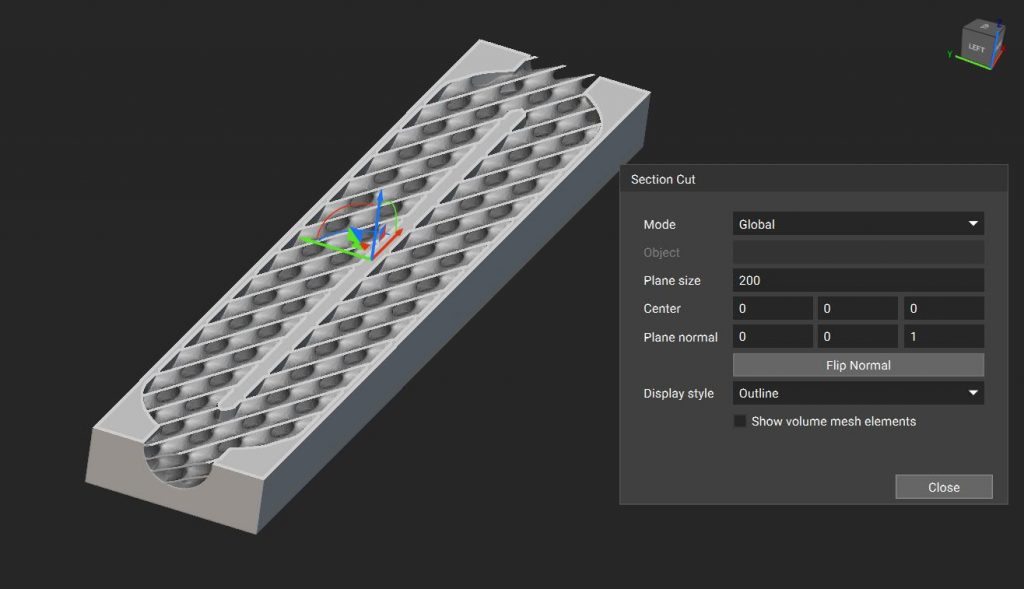
ANSYS Test Simulations
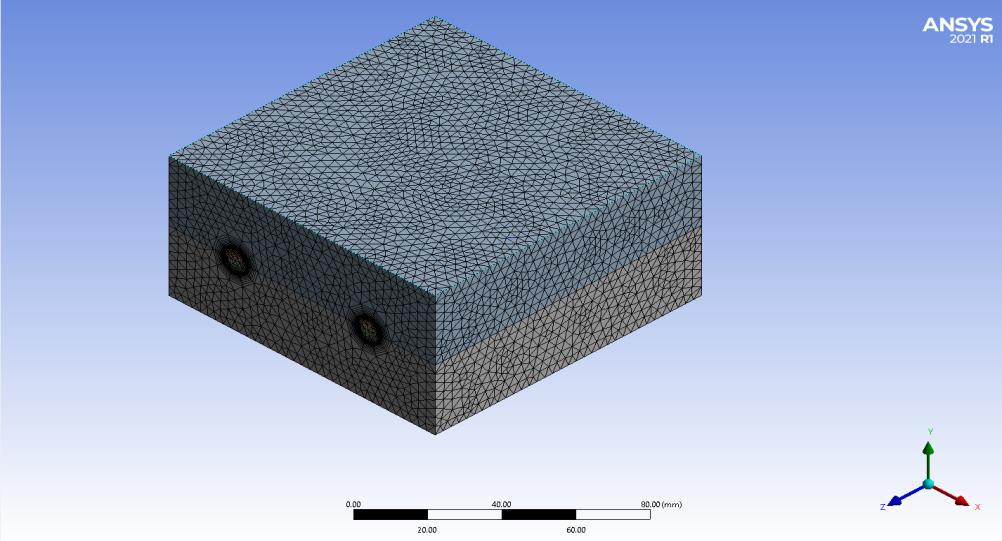
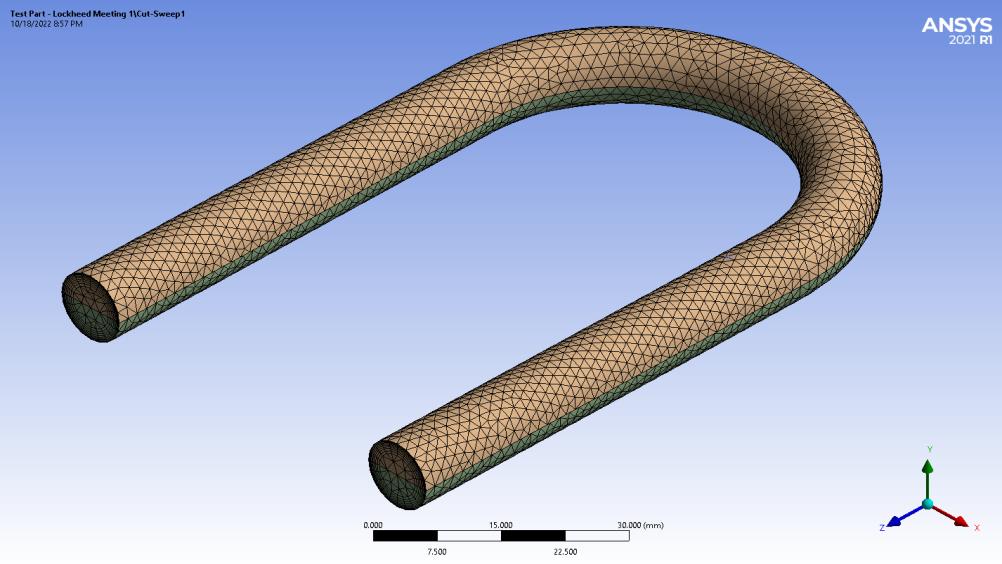
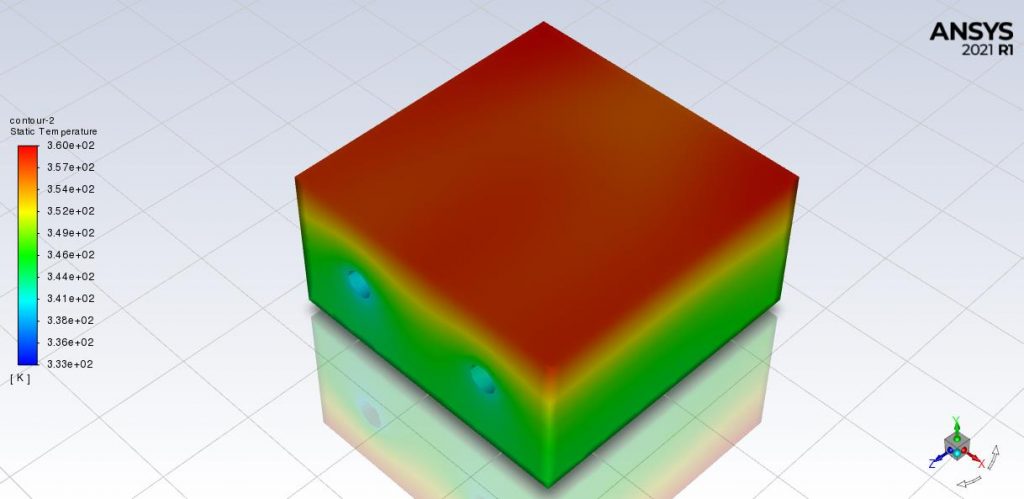
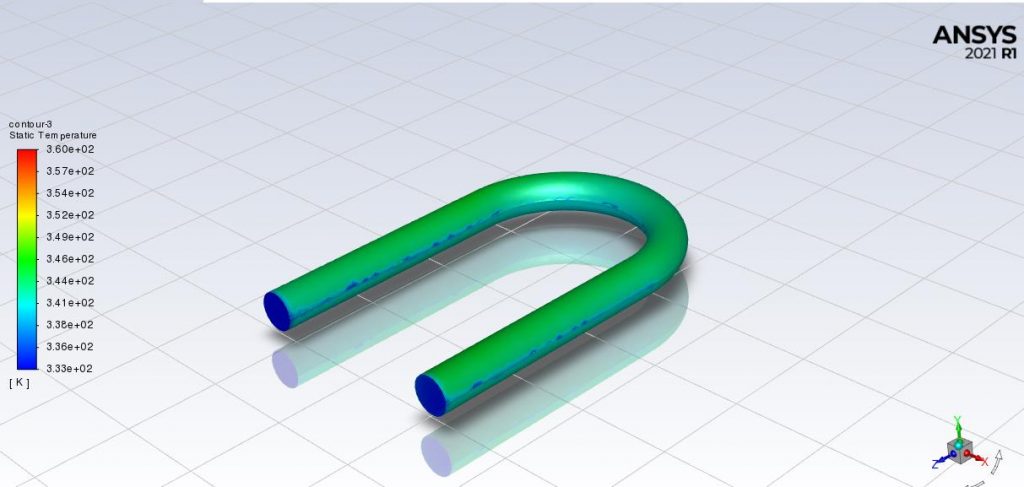
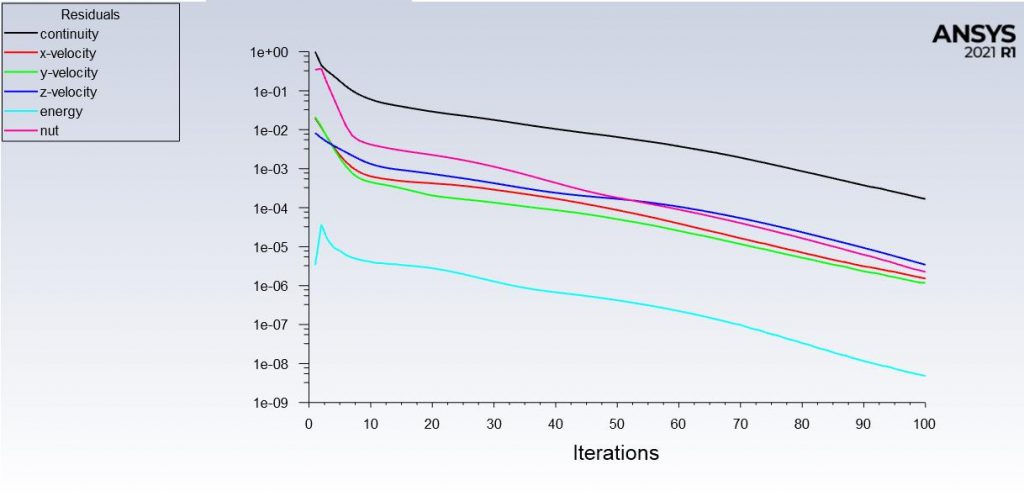
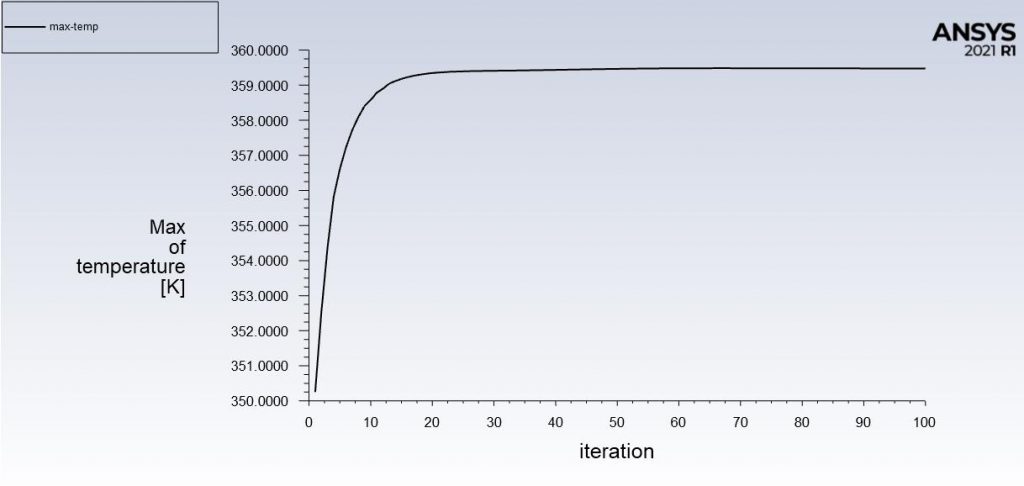
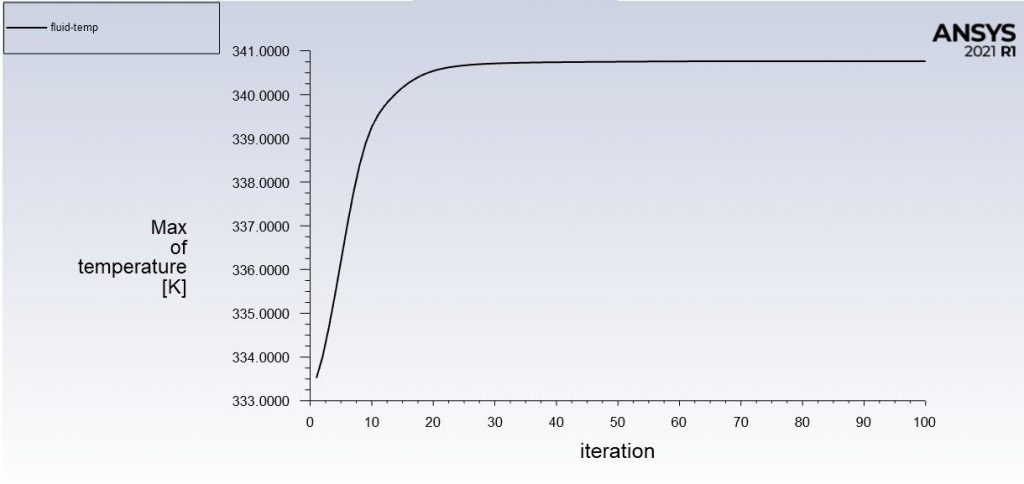
Deliverables
- Produce an additively manufactured cold plate with dimensions of 1.5 in x 8 in
- Decrease the cost to produce as well as minimize the volume of material used while remaining within the boundary conditions
- Responsible for modeling, analysis, and production of the product
- Perform preliminary design review as well as critical design review for Lockheed Martin
Team members
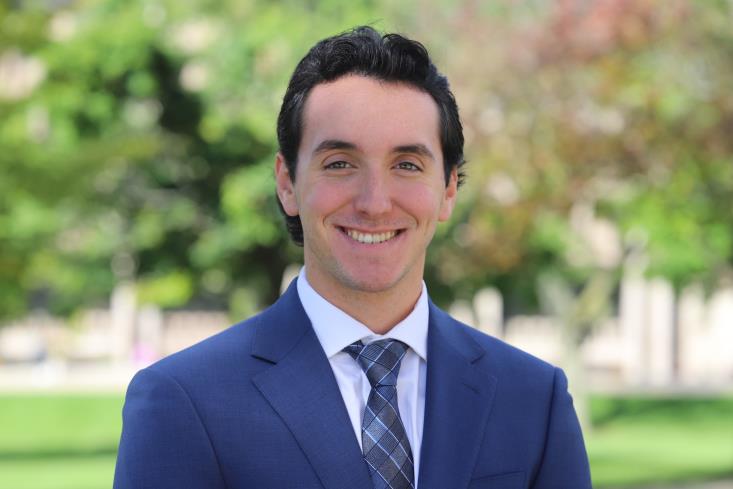
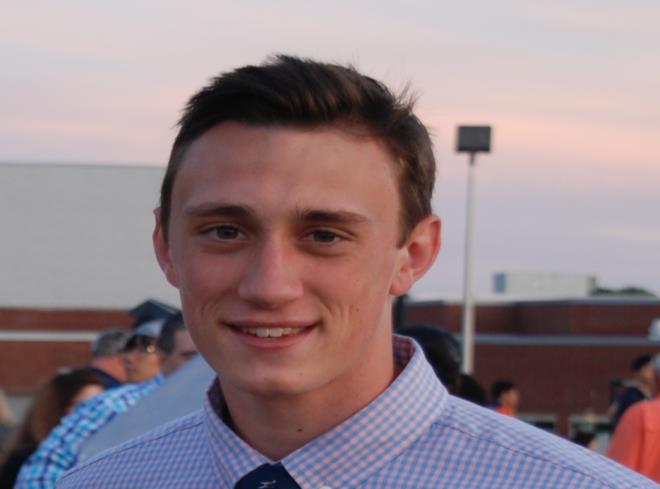
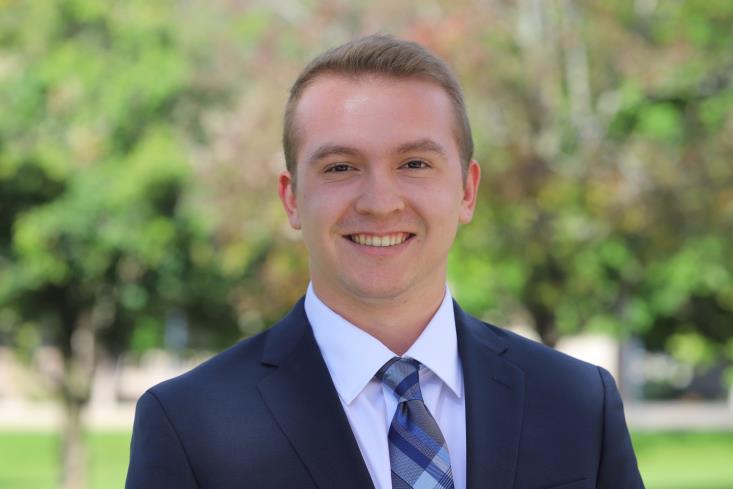
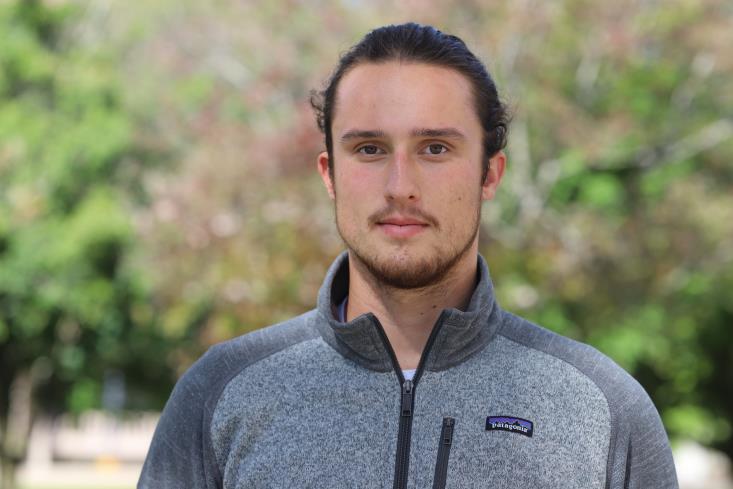
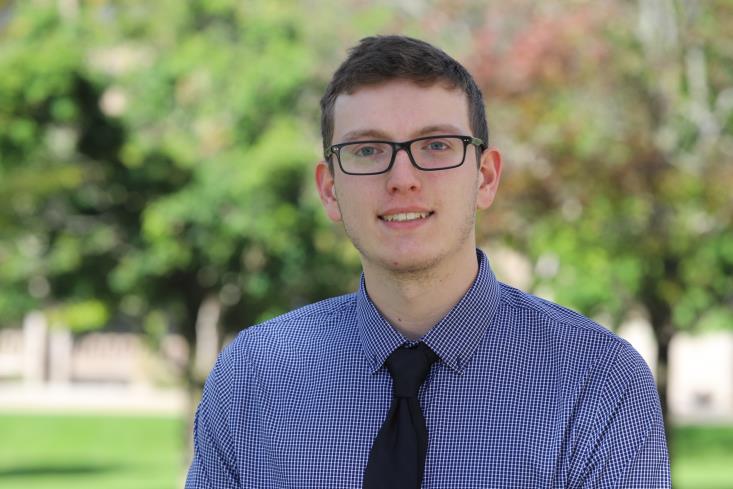
Faculty mentor
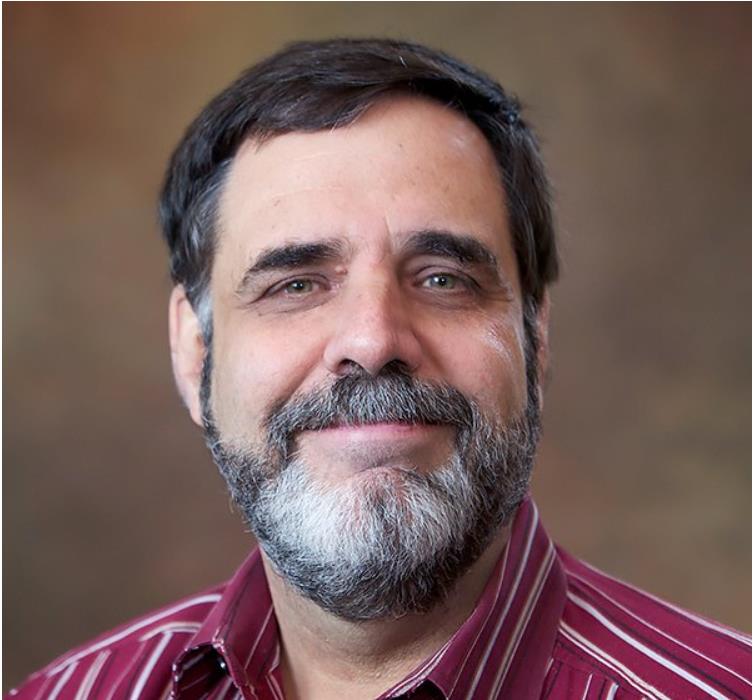