Project Description

Helium compressor packages made by Cryomech use desiccant adsorbers to “clean” helium as it is cooled to temperatures as low as 4K. Currently, the molecular sieve and granular activated charcoal used in the adsorbers is being contaminated from atmospheric exposure. Cryomech has asked the team to design an improved hopper system which will keep the desiccants clean and reduce production time.
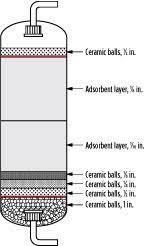
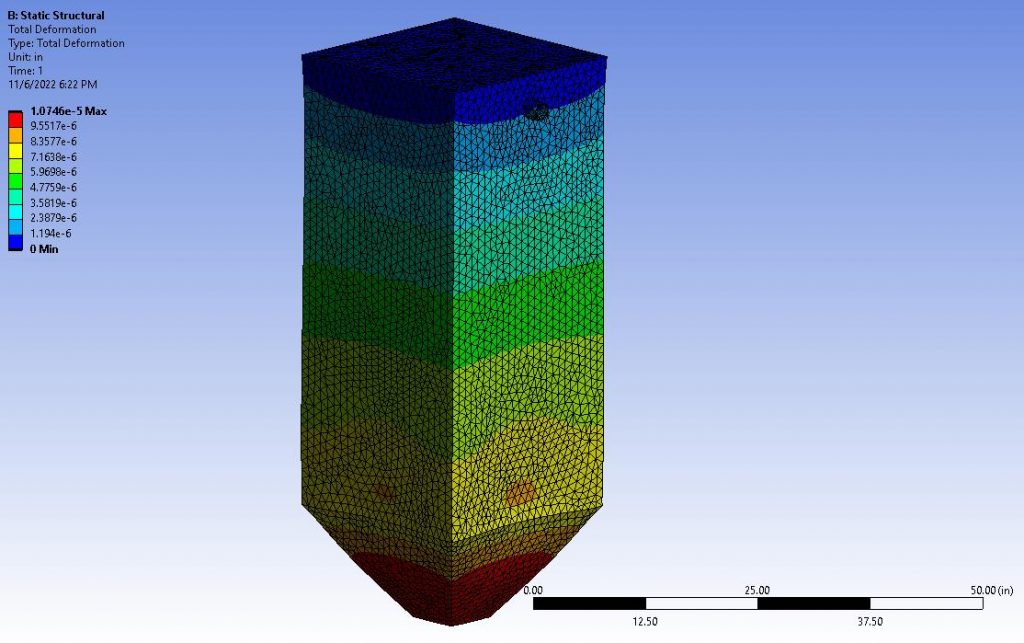
Possible Solutions:
The current solution that we have developed has four main components:
- Structure and Storage
- The size of the hoppers will be able to store one weeks worth of desiccants based on maximum production scenarios
- A nitrogen purge process if being investigated to passively clean the desiccants while in the hopper
- Material Transportation
- Material will be loaded into the hoppers via a compressed air conveying system
- This process will take under one hour and will reduce the required physical labor for the technician
- Heating
- Electrical resistance heaters either in the form of jackets or wire will be used to achieve the target temperature of 300℉
- The entire hopper will be covered with a layer of insulation to prevent heat loss
- Dispensing
- An injection molding starve feeder will be used to supply precise volumetric amounts of material.
Deliverables
- Automated dispensing system with 10 different volume configuration settings.
- Larger hopper size for refilling materials (granular activated charcoal, molecular sieve) less frequently than the current system. (Refilling once a week is desired)
- Hanging/elevated hopper toward the rooftop for saving space and user’s comfort.
- 300 F is desired for the hopper’s inner temperature.
- Reduce contamination of material to decrease the run-in time during production.
Team members
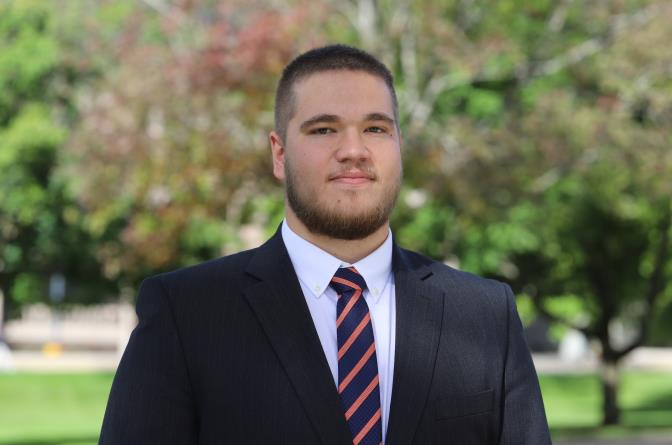
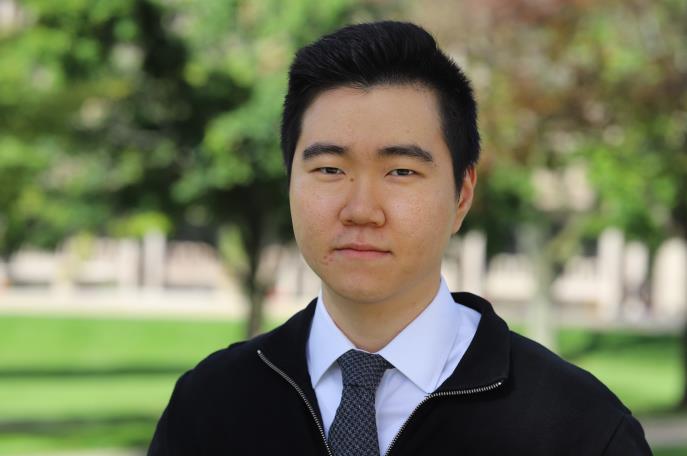
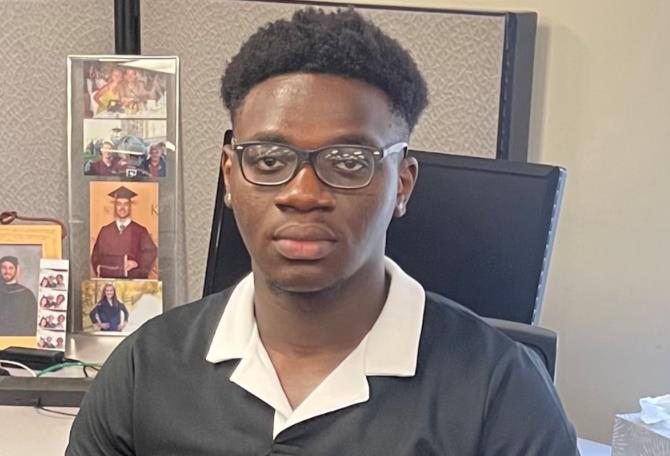
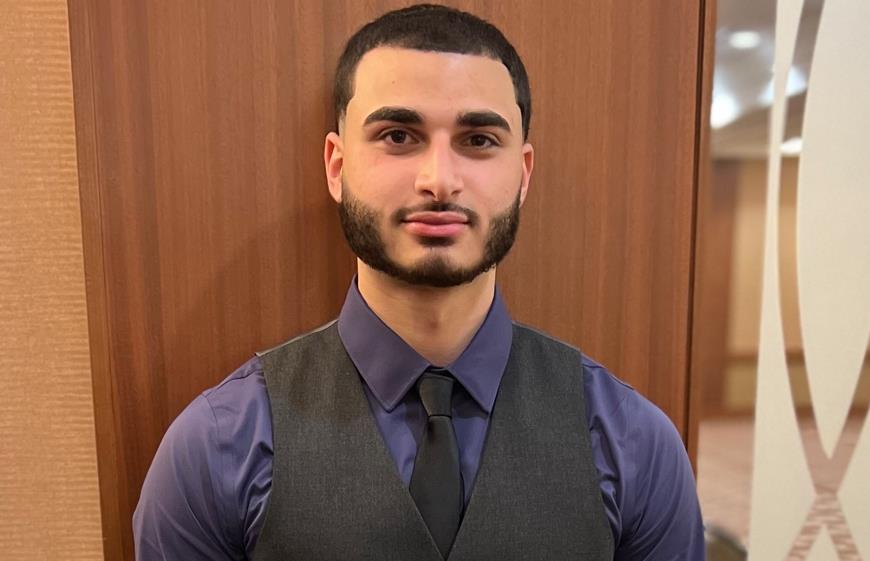
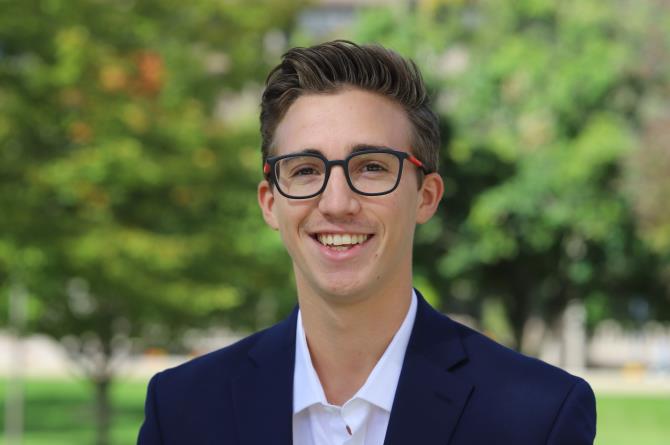
Faculty Mentor
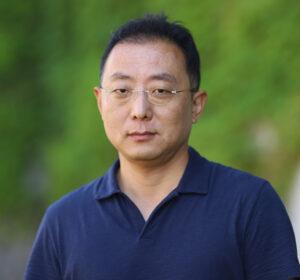